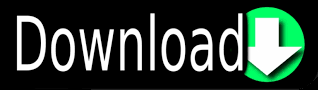
This information is necessary for the design of the turbocharger using new materials. This will improve the accuracy of the simulations and will give an insight of the temperature distribution of the housing. Therefore, future work will concentrate on extending the numerical model to include the conjugate heat transfer in the housing of the turbocharger. Additionally, the accuracy is limited by defining the walls as adiabatic. Reasons for the errors lie in geometry simplifications and the numerical model. However, lower speeds result in a significant overestimation compared to the experimental measurements. The isentropic efficiency is met quite well for 147,000 min −1. The slopes and the choke limit were predicted well, though. The results of the turbocharger simulation showed an overestimation of up to 10 % of the total pressure ratio for all operation points. However, the flow angle distribution revealed minor errors compared to the measured data.
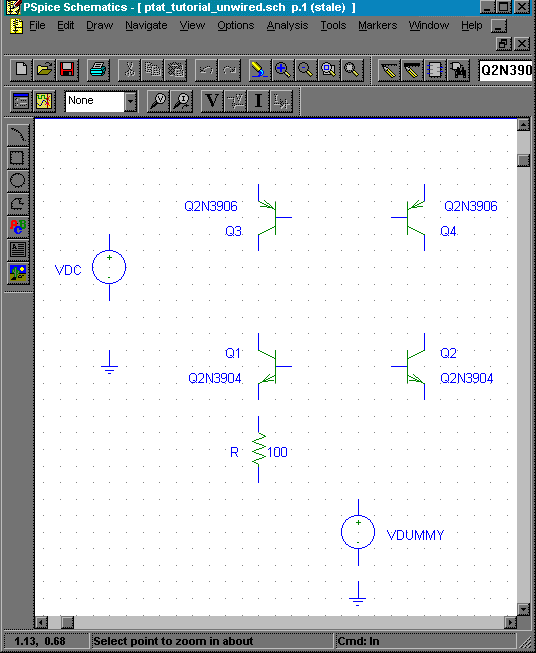
In the first case, both the impeller total pressure ratio and the adiabatic efficiency showed a very good agreement between simulation and experimental results. Secondly, the compressor side of a turbocharger was modelled including ported shroud and volute. The solver was first validated against the NASA low speed centrifugal compressor. The solver utilizes the multiple reference frame approach and local time stepping. Schwarze, in 8th International Conference on Compressors and their Systems, 2013 5 CONCLUSIONĪ pressure-based solver for turbomachinery application was presented using the open source library OpenFOAM.
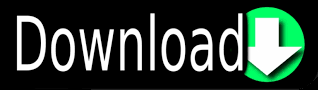